Earlier this year we started the Quest for Sustainability, a video series about creating a more sustainable product. Now I'm implementing some new things, starting off with a big one: a new factory!
Some Background
Honestly, when I started this journey, I was thinking that we'd just make our bags out of recycled polyester or something. I was thinking that sustainability would be box that I could check and then move onto the next thing. It didn't take long for me to realize that I was thinking of everything too narrowly. Rather than just focusing on how to create a more sustainable product, I realized that the true challenge (and opportunity) was in creating a more sustainable company.
One of the biggest takeaways from all my research this spring was to not think of it as sustainability, but rather "supply chain excellence". Instead of me just selecting this material instead of that one, I needed to get the supply chain set up so that every person in every link was making sustainable decisions. And the best place to start was with our factory. Not that our existing factory was *bad*, it just wasn't going to help get us to the place in sustainability that I wanted to go.
Finding a new factory
During my trip to China this spring, I visited several factories that had already taken some "sustainability steps", like working with bluesign® certified suppliers. One factory in particular really stood out to me, a factory called Zhiming Bags.
Zhiming Bags focuses on small, outdoor brands with small order sizes. They pay their sewers a wage rather than piecework (which is when the sewer gets paid a set amount for each task - the most common way to pay) and offers other benefits uncommon in most sewing factories. It's owned by Nico, a Frenchman who has lived in China a long time, and because of that, most of their customers are small European outdoor brands. Europe has very strict environmental and sustainability standards, so kicking our sustainability factor up a notch is no problem here.
But can we afford this?
I knew as I was walking through the Zhiming Bags facility and talking with the team that they were the right fit for Po Campo. Yet, I was worried about price. Surely the small quantity orders, sustainable fabrics/materials, and extra attention to detail would make it price prohibitive for us, right?
Fortunately, they have been a great collaborative partner. They've helped us find efficiencies across our product line, and other cost savings, that made working with them a realistic option for us. (Well, at least until we got hit by the latest round of tariffs, but I'll save that for another day 😫)
Making the change
As a practice run, we gave them a small order for the holiday season. In the photos below, you'll recognize the Kinga Handlebar bag in Mosaic, plus a new pattern that we'll announce shortly. All of that went smoothly, so we'll be moving all of our production over to their facility for 2019. Very excited about this!
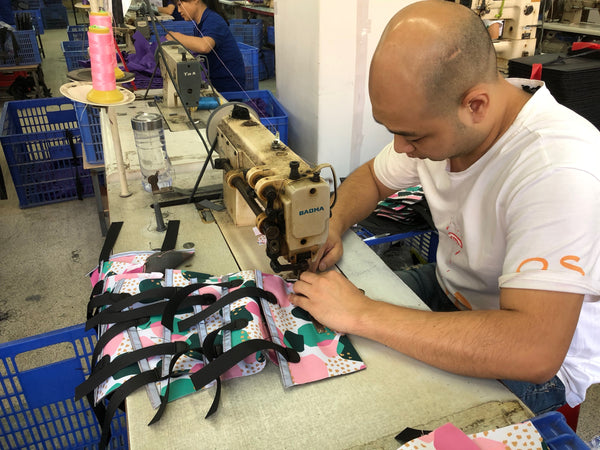
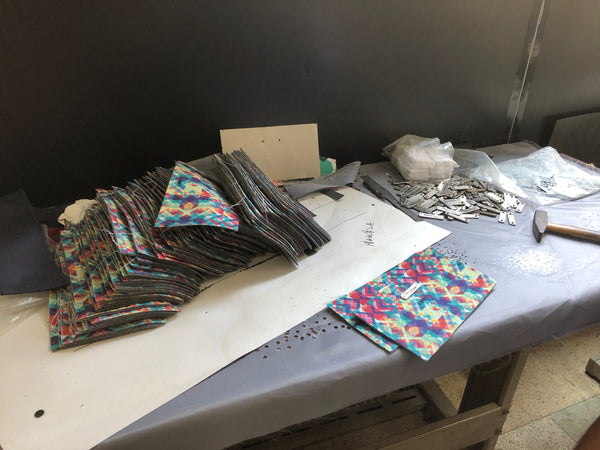